As we bulldozed into the 21st century, the construction industry has transformed itself with industrial machines and other heavy equipment, becoming more advanced and technologically enhanced. I ask three experts for their insights on how they view the technology that has transformed the likes of equipment like bulldozers, excavators, cranes and more, in the last five years.
Introduction by Daniel Gorlovetsky, CEO at TLVTech
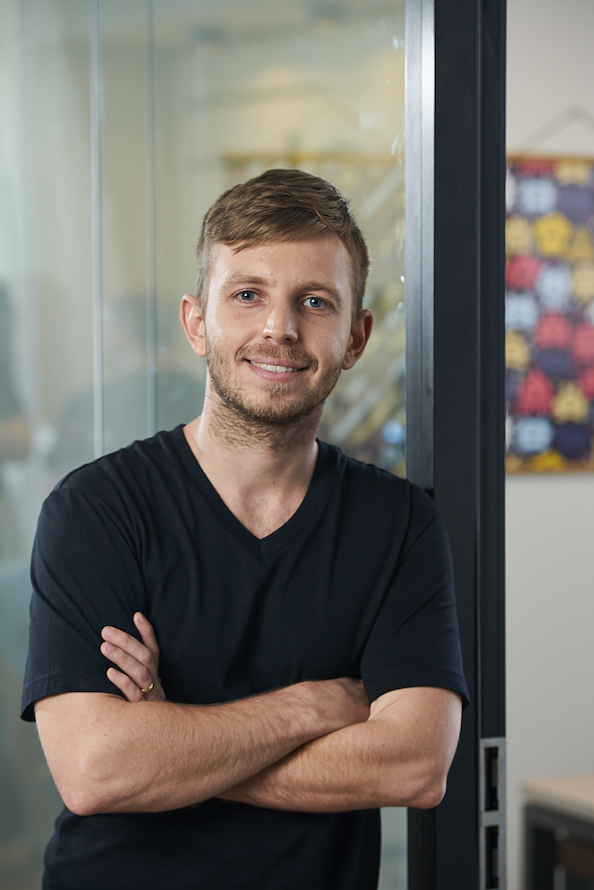
Over the last five years, the industrial construction machinery sector has experienced a seismic shift, driven by advancements in automation, electrification and connectivity.
Automation and autonomy
Modern construction machinery is increasingly autonomous. Excavators, bulldozers, and cranes now feature AI-powered control systems capable of executing complex tasks like grading, trenching and hauling with exceptional accuracy. These systems rely on a blend of GPS, Machine Learning and sensor fusion to navigate and operate in constantly changing environments. As a result, operators are transitioning from hands-on roles to supervisors who oversee operations and fine-tune system parameters across multiple machines. This shift enhances productivity, reduces labour dependency and minimises costly errors.
Electrification and sustainability
Electrification is rapidly gaining momentum—not only for environmental reasons but also for practical benefits like reduced noise and lower fuel costs. Advances in battery technology and charging infrastructure are making electric heavy machinery more feasible. In dense urban areas where emissions and noise regulations are strict, electric bulldozers and loaders are already proving their value. The trend is being reinforced by ESG mandates from both regulators and clients, making sustainability a competitive necessity rather than a niche concern.
Connectivity and smart operations
IoT and cloud-based connectivity have revolutionised equipment management. Real-time data enables predictive maintenance, remote diagnostics and performance tracking across entire fleets. This dramatically cuts down on unplanned downtime, improves cost efficiency and streamlines project timelines. Operators and managers can access machine health, location and usage stats from centralised dashboards, allowing better planning and resource allocation. Data has become a critical tool for informed decision-making in construction operations.
Safety innovations
Technology is also transforming safety protocols. Today’s smart machines are equipped with hazard detection systems, real-time alerts and emergency stop functions. Vision systems, LiDAR and even wearable tech are helping prevent collisions and monitor both machinery and personnel activity. These tools significantly reduce risk on-site and support compliance with increasingly rigorous safety standards.
The road ahead
The future of construction is one where machines autonomously adapt, optimize, and collaborate. Fully autonomous job sites—managed by AI and supervised by human operators—are no longer science fiction. The groundwork is already being laid, and at TLVTech, we’re proud to help lead the charge into this new era of intelligent construction.
Danilo Coviello, Founder of Espresso Translations
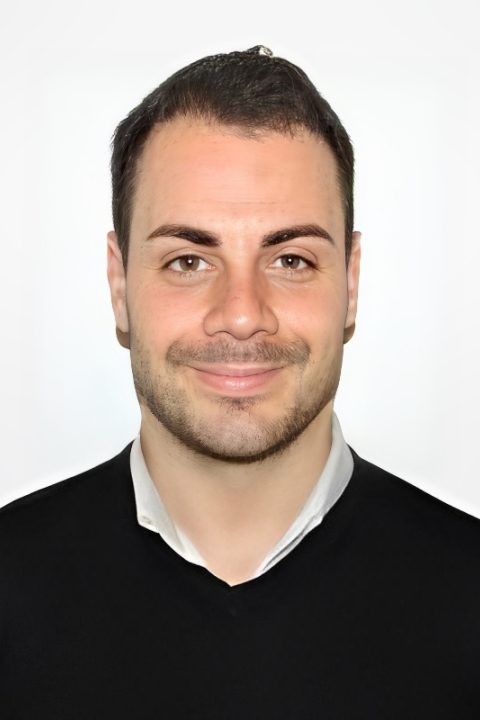
I am amazed by how technology revolutionised heavy construction equipment, with the previous five years bringing revolutionary innovation to operating machinery. Modern construction equipment fits advanced sensing systems and GPS components which allows these machines to operate with high precision. The accuracy of excavators has reached millimeter levels which substantially decreases the amount of work that must be repeated due to mistakes or lack of impact. GPS technology enables bulldozers to work at higher efficiency by following identified elevation paths which results in better task completion speed. Real-time monitoring systems on crane platforms operate automatically to modify load capacity boundaries therefore minimising any chance of exceeding limits. These technologies enable both speed improvement and reduce human error to deliver better quality outcomes at work.
The combination of machine learning has triggered the growth of predictive maintenance as an exciting development. Current industrial machinery gathers detailed information about engine temperature combined with hydraulic fluid pressure. Engine data from a bulldozer notifies operators about temperature elevations before failure occurs thus indicating potential underlying issues.
A previous project I worked on analysed our excavator data in real time to decrease unanticipated equipment breakdowns by 20% thus maintaining our construction schedules and budgets. The combination of automation alongside remote operation systems provides exceptional safety levels. Remote control operations now allow bulldozers to be managed from operators located miles away from the dangerous site. These machines now enable operations in dangerous environments thus protecting workers from actual harm. The real-time smart machine data stands out as the most important element because it enables project managers to deliver instant well-informed choices. The incorporation of these advanced systems leads to efficiencies across the board including fuel efficiency and time administration alongside new sustainable practices which seemed unattainable just a short time ago.
Craig Vander Galien, Founder of DrillerDB
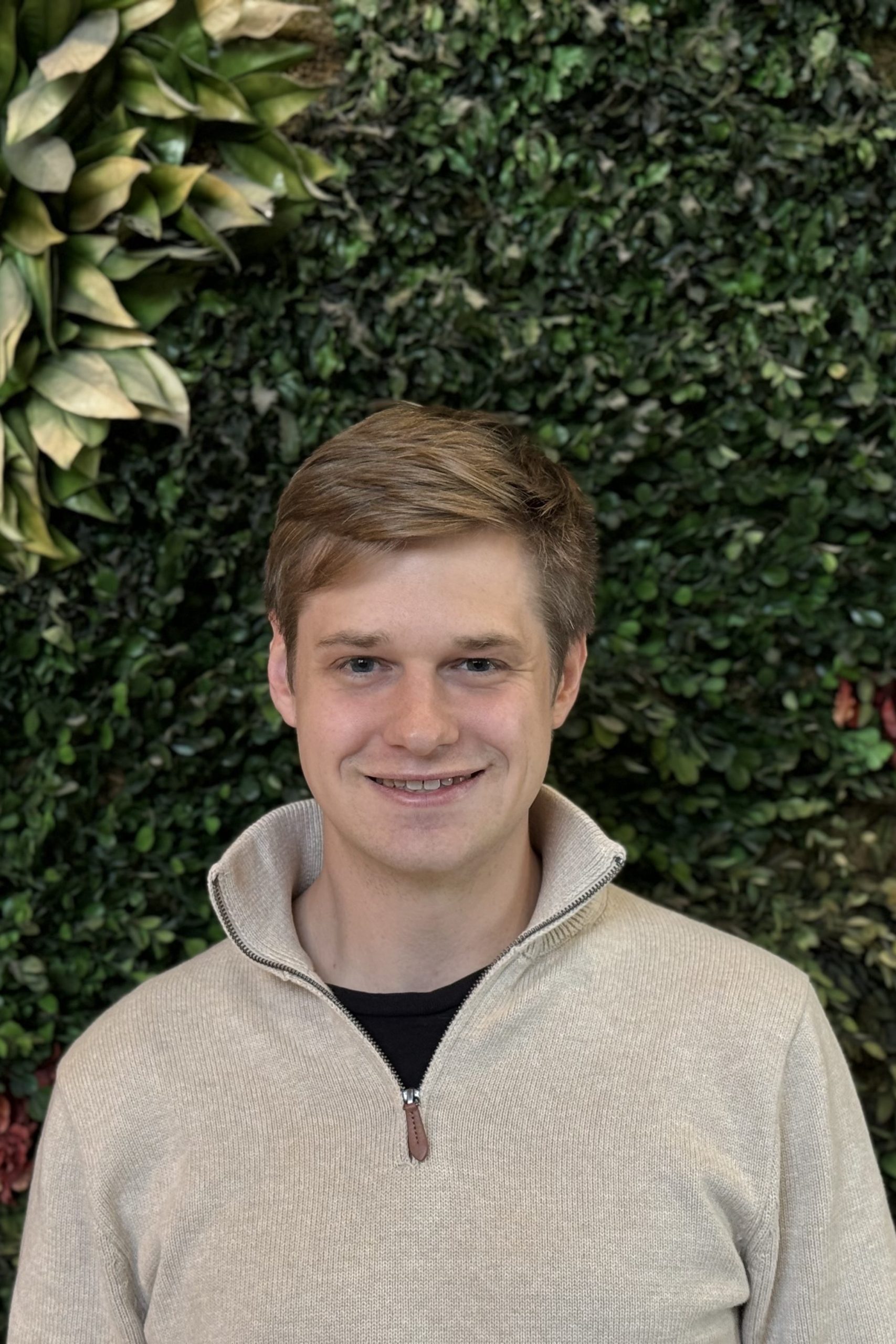
In my experience working in the field of Water Well Drilling over the past 12 years, I’ve noticed that water well drilling rigs – some of the largest road mobile equipment pieces – and their accompanying equipment haven’t changed much from the basic technology perspective of hydraulics, diesel engines and compressors.
However, what has changed is the technology around them: The smartphone revolution and Internet of Things has transformed how we track, dispatch and log data from these vehicles.
At our business, over the last five years we started tracking the locations of these vehicles with on-vehicle GPS trackers. Then we integrated that data into a dashboard that lets us track these vehicles alongside our current and upcoming project lists. This has helped us add efficiency in how we move this equipment from job to job, saving fuel and time. Before a live map we’d sometimes have to double back to a job we missed – no longer.
On top of that we use drilling data entered by our field crews – no longer relying on their memory at the end of the day filling out forms. Our drilling data is then uploaded to our software platform to facilitate faster reporting to the relevant government agencies.
We’ve even taken this a step further and integrated the state well log data to estimate drilling depths and geological conditions at any site. Our field crews as they are drilling through to the aquifer can reference the data from the well next door – right on their smartphone – so they know which type of rock they’ll be encountering next. No longer are they going in half blind as to what conditions they’ll be experiencing.
Recently we’ve started using AI features to get a broader picture of the drilling conditions in our area, painting a comprehensive picture of these drilling conditions for our heavy equipment.
We had to handle these integrations internally, however, as in our industry there was no single system that would enable this cross-integration. Sometimes if you want a solution that works for you, you need to build it yourself.
The next step, of course, is live data tracking from the equipment itself – logging how deep we are drilling and being able to feed that information back to headquarters – this would enable a better sense of when the drilling will be complete or if there have been any delays. This would enable clearer communication to the upcoming customers as to when we’ll be able to reach them.
To best utilise our heavy equipment over the last five years we’ve layered technology solutions at every level: from the vehicle itself to the operator’s smartphone, to our office systems.